- EnRob is an optimal solution in inspecting components of complicated forms made of carbon fiber.
- Consisting of dedicated sensors and 6-axis robotic arms, EnRob is capable of precisely scanning any form of carbon fiber component.
- Scanned data can be analyzed three dimensionally by means of the dedicated software program. Such data can be utilized in detecting and assessing the weaving directions and defects of a fiber.
EnRob
EddyCurrent NDT
Feature
- Nondestructive testing of defects inside carbon fiber components
- Sensor bundles provided for the measurement of the different materials
- Dedicated software programs for sensor and robot control
- 6-axis robots capable of precise scanning
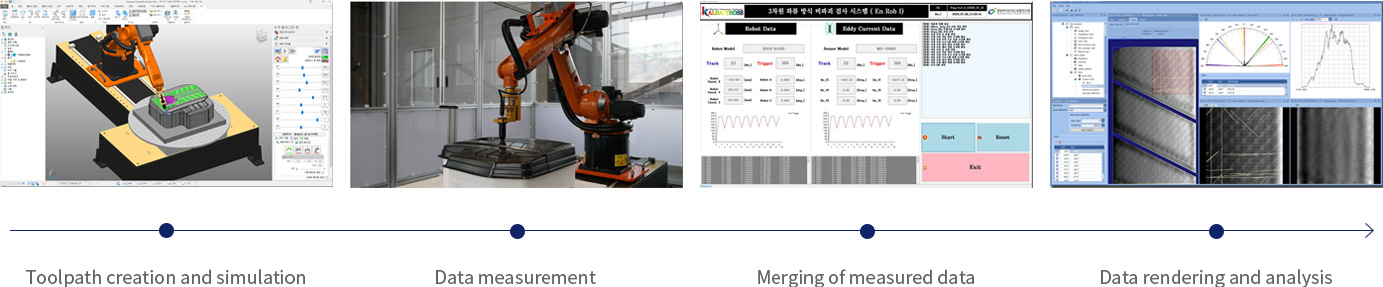
SPECIFICATION
Scroll left/right.
Classification | Major Specifications | |
---|---|---|
Equipment Configuration | 3 x Sensor | |
1 x Sensor Cord | ||
1 x Control Unit | ||
1 x Power Supply | ||
1 x Software library | ||
Sensor Format | High Spatial Resloution | |
High Penetration Resolution | ||
Weight | Weight of each sensor 130g | |
Sensor Cord 100g/m | ||
Control Cabinet 10kg | ||
Size | Each sensor 30 x 90㎜ (g/h) | |
Sensor Cord Length 1 ~ 5m |
||
Control Cabinet 300 x 300 x 150㎜ | ||
Range of sensor coil diameter | 1 ~ 7㎜ | |
Output data rate | 1 ~ 1,000 Samples/Second | |
Input trigger rate | 1 ~ 1000 ㎑@ 5V/24V | |
Range of sensor frequency | 1 ~ 30 ㎒ (other on request) | |
Power consumption | 70W | |
Integration | Library DLL for C# | |
Interface | UDP, TCP-UP, Modbus via Ethernet | |
Required conditions | 10℃ - 40℃ IPS |
- En Rob* System - Sensor Package Specifications